A smart factory is a pretty modern thing. To make it work, it needs a few basic operational and technical requirements. In this section you will learn what a smart factory absolutely needs. You will see that this is quite a lot!
Important
The data exchange
The requirements start with the data exchange itself. A smart factory exchanges a large amount of information. This data exchange must be able to run according to the following basic rules:
Bidirectional data transfer
Information exchange works in both directions (both sending and receiving information).
Horizontal and vertical data transfer
Information is exchanged both vertically across different departments (e.g.: customer order management, factory floor, product) and horizontally (machine A to machine B on the factory floor).
Since the goal is to record important process data in production in real time, operational control systems must be integrated in the data exchange. These operational control systems are concepts that help to manage, monitor and control companies in the production sector. The following must be included:
Enterprise Resource Planning
This is where resources, such as material and operating equipment, but also personnel, capital and general information technology, are planned, controlled and managed.
Manufacturing Execution
This refers to the control and monitoring of real-time production (also referred to in German as production control system).
Product Lifecycle Management
A concept that deals with the lifecycle (from design, construction and production to sale, use and disposal) and the management of the information generated in the process.
Supply chain management
The management and improvement of the supply chain, i.e. the delivery and receipt of production and service goods.
Of course, technological building blocks and prerequisites are also needed for a smart factory to function in real time. Some of the most important are already developed and in use. These are very general components such as sensors (“sensing elements” that can detect physical or chemical properties of their environment) and actuators (components that perform mechanical movements when electrically controlled). Modern, automatable production techniques such as robotics and 3D printing are important here, but also various operational IT applications, e.g. for production management and controlling. Networking via broadband Internet and control via cloud systems (external servers that provide computing power) are already technically possible.
However, other systems and components are still in their infancy, such as augmented reality – here the perceived reality is “extended” with the information from a computer (e.g. Google Glass). The following table gives a brief overview of the required technological building blocks:
Excursus
Industry and factories in transition
If you define smart factory as a part of Industry 4.0 it is obvious that there must have been an Industry 1.0, 2.0 and 3.0.
While the first and second stages of industrialisation led to the introduction of mechanical production facilities and mass production, Industry 3.0 was already about automation, the use of IT and electronics – but without these components communicating with each other in real time and influencing each other.
As just mentioned, some of the necessary technologies are already in use as further developments of these industrial precursors, but others have yet to be developed from scratch. There are also influences from non-industrial areas. The “Internet of Things” plays a major role here and is already more widely known in the private sector than the networking of household appliances (example: mobile phone recognises that you are coming home and automatically switches on the lights in the apartment, at the same time the coffee machine makes an espresso and the TV turns on the news).
Industry 4.0 must take Internet of Things technologies to an industrial level and put them into an economically profitable framework. This is the only way a truly new and fourth “industrial revolution” can succeed.
Of course, at first glance, many of these technologies are somewhat opaque in terms of meaning and function. Therefore, the most important ones will be explained in more detail in the following:
Cyber physical systems (CPS)
First things first: CPS are the technical cornerstone of every smart factory. Also known as embedded systems, this refers to any electronic and information technology equipment of objects in the production environment. These can be:
Sensors, for the direct environment of the object
Actuators that actively move objects (for example levers)
Identifiers to uniquely identify and assign objects (e.g. barcode)
Microcontrollers (chips mentioned above), which analyse data, determine the status and determine the next steps
Communication systems that allow access to the network via cable or radio
This is what makes an object “smart” – in other words, intelligent. Examples of such smart objects in the production environment are tools or intelligent containers. Such a container can be identified via its barcode and provides information about its position and contents via sensors and microcontrollers.
IPv6 – many, many Internet addresses
Another basis for Smart Factory development is a new Internet protocol. Such a protocol can ensure a sufficiently large so-called “address space”. The more intelligent objects are connected to each other, the more Internet addresses are needed to address them unmistakably.
Broadband networks
Smart factories generate, send, receive and process a vast amount of data. This must happen quickly – otherwise it is not possible to work in real time. This requires broadband networks to ensure sufficiently high data transfer rates, keep delay times low and provide fail-safe operation.
Important
WLAN and mobile communications
To put it simply, of course, a strong WLAN is required internally – but outside the company, mobile phone networks must also be considered (example: a truck that automatically informs the receiving factory of a traffic jam and thus delayed resources via mobile phone).
Machine-to-machine communication (M2M) – intelligent machines
Other technological building blocks are interacting machines that can automatically exchange information with other machines and the products. Material data, order information, the current status and maintenance measures are communicated. They also collect data about their system status – in principle, “how they are doing”. Thus, ongoing processes can be analysed and (re-)controlled in real time.
Human-Machine-Interfaces (HMI)
The interaction of man, machine and product (note: in real smart factories all three must be intelligent) is particularly exciting. While highly mobile devices such as tablets and smartphones already offer direct human integration into the network and communication of a smart factory, there is still a lot of scope for research in this area.
A highly contemporary, alternative method is the isolated use of Augmented Reality glasses, which provide the employees in the production environment with additional virtual information.
Production control systems – Manufacturing Execution Systems (MES)
These have already been mentioned above in the operational control systems and are used for the management of resources (operating resources, personnel and delivery parts) and for the comprehensive recording of production data (operating, machine and personnel data).
Such production control systems have existed for a very long time, but they are not yet fully networked. Once they are able to exchange information in real time with production plants, logistics systems and products, the full potential of a smart factory is released.
Big Data Analytics
If everything and everyone generates, processes and sends data in real time, then of course enormous amounts of data result – these want and need to be handled properly by appropriate IT infrastructure and IT equipment. Further analysis also requires a high computing capacity.
Big Data Management and Big Data Analytics are already offered on the market with standard solutions or are carried out as an integrated cloud solution – but the requirements are constantly increasing.
Cloud computing and storage space
Cloud computing refers to the external use of computing power and storage space made available via an Internet or Intranet. Given the high demands on data performance, integrating a “cloud” in a production environment is not a bad idea. This allows all applications and data to be managed and coordinated centrally.
Previously used in-house server solutions can no longer meet the demands of big data processing and the requirements of a smart factory for analysis, planning, controlling and optimisation in real time.
Important
And the human?
In this chapter you have learned that production should largely operate without humans, but now again that humans are integrated via augmented reality – well, now what?
Well, even if the smart factory is supposed to be fundamentally self-organising and automate the manufacturing process, the human being is still a part of it – just not in the role of production, but of further optimisation and control of the manufacturing systems. In doing so, they coordinate interfaces to other systems or production environments, for example. Augmented reality as a concept is also important here – it enables virtual intervention without any physical contact.
A smart factory also needs generalised standards and norms. A common semantic basis (i.e. compatible programming languages and a universal production language) is absolutely necessary. A standardisation of smart factory operations can prevent systems that should communicate with each other from not understanding each other in the end due to technological differences.
Example
Legal challenges in the smart factory
Rapid technological developments also raise legal issues, some of which have not yet been fully resolved. An example illustrates the problem:
A vendor receives a purchase order from a company. The company processes Plasticine into funny animals and then sells them to toy shops. The company uses a smart factory, which means it is automatically networked with both, the supplier (raw modelling clay) and the customers (toy store). However, a purchase order was sent because the system incorrectly processed customer demand and is much higher than the company can process or store. Of course, the company does not want to pay the surplus, the toy retailers do not need such a huge amount of Plasticine anyway and the supplier is angry because he produced Plasticine for free.
Who is to blame now? Who must pay if the mistake has caused a system that involves all three parties? Here the law is not yet interpreted clearly enough.
In addition, the question of data protection, compliance and secrecy within partnerships arises. When all data is exchanged, everything is disclosed at the same time. For example, which of the data made available may be used by the supplier? For what purpose? Here, too, concepts still need to be developed.
Remember
Smart factory requires some operational and technical prerequisites to enable the desired networking and real-time data exchange.
The main technological building blocks are:
Cyber-Physical-Systems
Big Data and Cloud Computing
Broadband and sufficient address space
Human Machine Interfaces
Integration of operational production control systems
Man is no longer a part of production, but controls and optimises the production processes.
Smart factories must also be considered within a legal framework – standards and norms can help here.
A smart factory is a pretty modern thing. To make it work, it needs a few basic operational and technical requirements. In this section you will learn what a smart factory absolutely needs. You will see that this is quite a lot!
Important
The data exchange
The requirements start with the data exchange itself. A smart factory exchanges a large amount of information. This data exchange must be able to run according to the following basic rules:
Information exchange works in both directions (both sending and receiving information).
Information is exchanged both vertically across different departments (e.g.: customer order management, factory floor, product) and horizontally (machine A to machine B on the factory floor).
Since the goal is to record important process data in production in real time, operational control systems must be integrated in the data exchange. These operational control systems are concepts that help to manage, monitor and control companies in the production sector. The following must be included:
This is where resources, such as material and operating equipment, but also personnel, capital and general information technology, are planned, controlled and managed.
This refers to the control and monitoring of real-time production (also referred to in German as production control system).
A concept that deals with the lifecycle (from design, construction and production to sale, use and disposal) and the management of the information generated in the process.
The management and improvement of the supply chain, i.e. the delivery and receipt of production and service goods.
Of course, technological building blocks and prerequisites are also needed for a smart factory to function in real time. Some of the most important are already developed and in use. These are very general components such as sensors (“sensing elements” that can detect physical or chemical properties of their environment) and actuators (components that perform mechanical movements when electrically controlled). Modern, automatable production techniques such as robotics and 3D printing are important here, but also various operational IT applications, e.g. for production management and controlling. Networking via broadband Internet and control via cloud systems (external servers that provide computing power) are already technically possible.
However, other systems and components are still in their infancy, such as augmented reality – here the perceived reality is “extended” with the information from a computer (e.g. Google Glass). The following table gives a brief overview of the required technological building blocks:
Excursus
Industry and factories in transition
If you define smart factory as a part of Industry 4.0 it is obvious that there must have been an Industry 1.0, 2.0 and 3.0.
While the first and second stages of industrialisation led to the introduction of mechanical production facilities and mass production, Industry 3.0 was already about automation, the use of IT and electronics – but without these components communicating with each other in real time and influencing each other.
As just mentioned, some of the necessary technologies are already in use as further developments of these industrial precursors, but others have yet to be developed from scratch. There are also influences from non-industrial areas. The “Internet of Things” plays a major role here and is already more widely known in the private sector than the networking of household appliances (example: mobile phone recognises that you are coming home and automatically switches on the lights in the apartment, at the same time the coffee machine makes an espresso and the TV turns on the news).
Industry 4.0 must take Internet of Things technologies to an industrial level and put them into an economically profitable framework. This is the only way a truly new and fourth “industrial revolution” can succeed.
Of course, at first glance, many of these technologies are somewhat opaque in terms of meaning and function. Therefore, the most important ones will be explained in more detail in the following:
Cyber physical systems (CPS)
First things first: CPS are the technical cornerstone of every smart factory. Also known as embedded systems, this refers to any electronic and information technology equipment of objects in the production environment. These can be:
This is what makes an object “smart” – in other words, intelligent. Examples of such smart objects in the production environment are tools or intelligent containers. Such a container can be identified via its barcode and provides information about its position and contents via sensors and microcontrollers.
IPv6 – many, many Internet addresses
Another basis for Smart Factory development is a new Internet protocol. Such a protocol can ensure a sufficiently large so-called “address space”. The more intelligent objects are connected to each other, the more Internet addresses are needed to address them unmistakably.
Broadband networks
Smart factories generate, send, receive and process a vast amount of data. This must happen quickly – otherwise it is not possible to work in real time. This requires broadband networks to ensure sufficiently high data transfer rates, keep delay times low and provide fail-safe operation.
Important
WLAN and mobile communications
To put it simply, of course, a strong WLAN is required internally – but outside the company, mobile phone networks must also be considered (example: a truck that automatically informs the receiving factory of a traffic jam and thus delayed resources via mobile phone).
Machine-to-machine communication (M2M) – intelligent machines
Other technological building blocks are interacting machines that can automatically exchange information with other machines and the products. Material data, order information, the current status and maintenance measures are communicated. They also collect data about their system status – in principle, “how they are doing”. Thus, ongoing processes can be analysed and (re-)controlled in real time.
Human-Machine-Interfaces (HMI)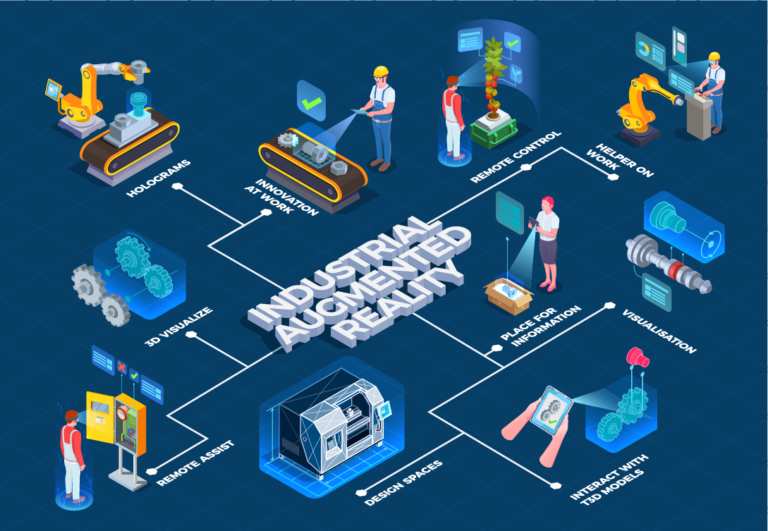
The interaction of man, machine and product (note: in real smart factories all three must be intelligent) is particularly exciting. While highly mobile devices such as tablets and smartphones already offer direct human integration into the network and communication of a smart factory, there is still a lot of scope for research in this area.
A highly contemporary, alternative method is the isolated use of Augmented Reality glasses, which provide the employees in the production environment with additional virtual information.
Production control systems – Manufacturing Execution Systems (MES)
These have already been mentioned above in the operational control systems and are used for the management of resources (operating resources, personnel and delivery parts) and for the comprehensive recording of production data (operating, machine and personnel data).
Such production control systems have existed for a very long time, but they are not yet fully networked. Once they are able to exchange information in real time with production plants, logistics systems and products, the full potential of a smart factory is released.
Big Data Analytics
If everything and everyone generates, processes and sends data in real time, then of course enormous amounts of data result – these want and need to be handled properly by appropriate IT infrastructure and IT equipment. Further analysis also requires a high computing capacity.
Big Data Management and Big Data Analytics are already offered on the market with standard solutions or are carried out as an integrated cloud solution – but the requirements are constantly increasing.
Cloud computing and storage space
Cloud computing refers to the external use of computing power and storage space made available via an Internet or Intranet. Given the high demands on data performance, integrating a “cloud” in a production environment is not a bad idea. This allows all applications and data to be managed and coordinated centrally.
Previously used in-house server solutions can no longer meet the demands of big data processing and the requirements of a smart factory for analysis, planning, controlling and optimisation in real time.
Important
And the human?
In this chapter you have learned that production should largely operate without humans, but now again that humans are integrated via augmented reality – well, now what?
Well, even if the smart factory is supposed to be fundamentally self-organising and automate the manufacturing process, the human being is still a part of it – just not in the role of production, but of further optimisation and control of the manufacturing systems. In doing so, they coordinate interfaces to other systems or production environments, for example. Augmented reality as a concept is also important here – it enables virtual intervention without any physical contact.
A smart factory also needs generalised standards and norms. A common semantic basis (i.e. compatible programming languages and a universal production language) is absolutely necessary. A standardisation of smart factory operations can prevent systems that should communicate with each other from not understanding each other in the end due to technological differences.
Example
Legal challenges in the smart factory
Rapid technological developments also raise legal issues, some of which have not yet been fully resolved. An example illustrates the problem:
A vendor receives a purchase order from a company. The company processes Plasticine into funny animals and then sells them to toy shops. The company uses a smart factory, which means it is automatically networked with both, the supplier (raw modelling clay) and the customers (toy store). However, a purchase order was sent because the system incorrectly processed customer demand and is much higher than the company can process or store. Of course, the company does not want to pay the surplus, the toy retailers do not need such a huge amount of Plasticine anyway and the supplier is angry because he produced Plasticine for free.
Who is to blame now? Who must pay if the mistake has caused a system that involves all three parties? Here the law is not yet interpreted clearly enough.
In addition, the question of data protection, compliance and secrecy within partnerships arises. When all data is exchanged, everything is disclosed at the same time. For example, which of the data made available may be used by the supplier? For what purpose? Here, too, concepts still need to be developed.
Remember
Smart factory requires some operational and technical prerequisites to enable the desired networking and real-time data exchange.
The main technological building blocks are:
Man is no longer a part of production, but controls and optimises the production processes.
Smart factories must also be considered within a legal framework – standards and norms can help here.